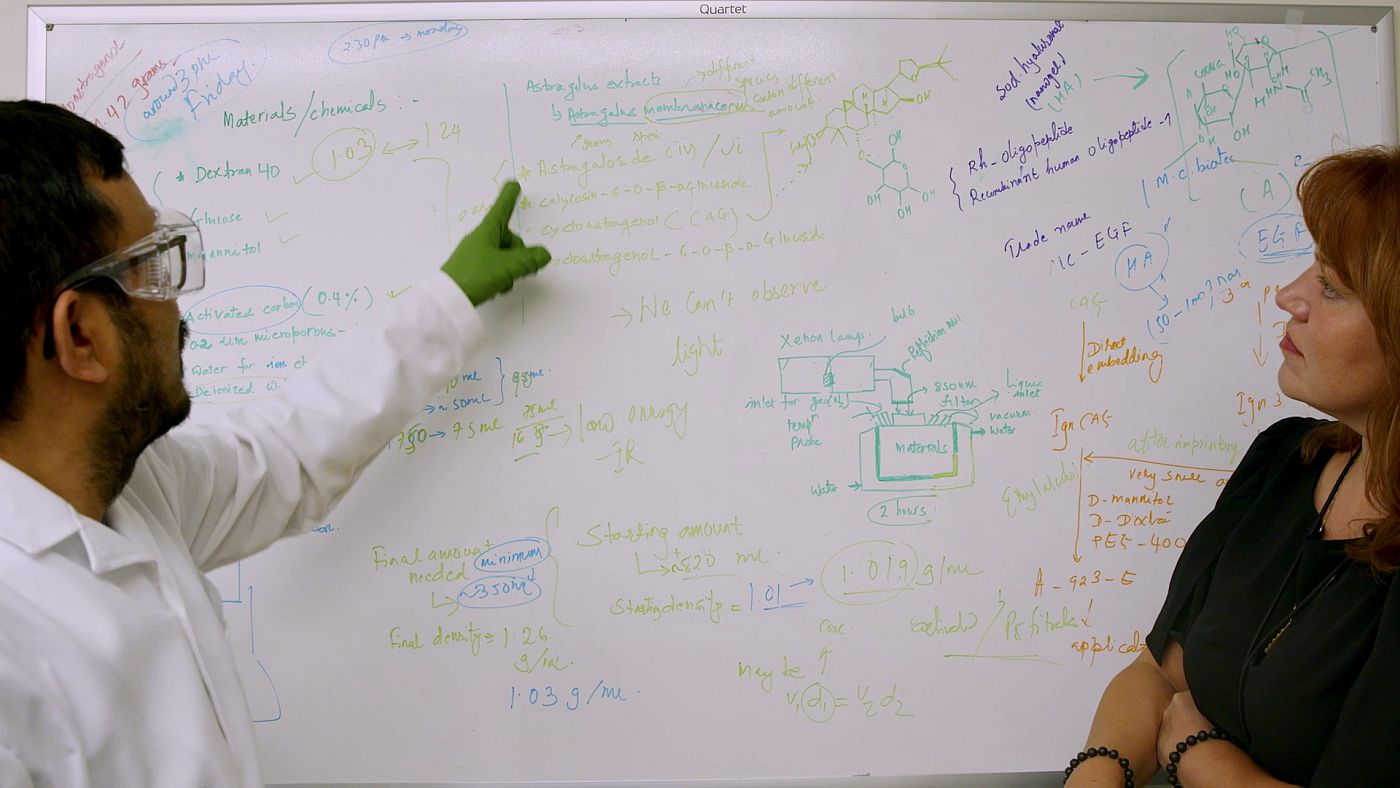
Telomeron Inc, a US-based company owned 90% by Exagon Industries Ltd and 10% by Gaia Inc (NASDAQ:GAIA), has made a significant breakthrough with its TELOS-SP technology. The company, established in 2016, focuses on developing technology strategies for molecular surface treatment.
Today, Telomeron Inc has announced that it has successfully modified active ingredient molecules targeted at the cosmeceutical and nutraceutical sectors using a new class of quasi-particles called Ignitons, generated through the interaction between laser photons and ions in a low-pressure plasma environment. This technology has been proven through clinical trials, showing a 40% increase in absorption factors in some cases.
Telomeron Inc is not limiting itself to anti-aging and cosmetic products but plans to extend its technology to the food, agro-technical, and zootechnical supplementation sectors.
To achieve this, the company plans to externalize formulation, manufacturing, and packaging, while internalizing the processing of the blend with proprietary technology and product sales & marketing activities. Exagon group has approached industrial and institutional investors for funding to further develop Telomeron Inc towards a structure capable of offering B2B embedding services and dedicated B2C product lines.
Exagon has engaged Arthur D Little USA and Europe to develop appropriate business plans, market analysis, and investor scouting and fundraising activities. The ultimate goal is to divest the majority of its Telomeron shares to institutional and industrial investors capable of supporting its development, with the aim of projecting Telomeron towards a future listing on the public market, increasing its value to at least US$2 billion. The technology is scalable and not retro-engineerable, giving Telomeron multiple advantages and opportunities for future growth in various industries.

The interaction of photons and electrons in a cloud of high-energy compressed plasma is fundamental to the process. The system's architecture is currently classified, and no disclosures or publications on the technology behind the system will be issued.
Interactions between light, electrons, and matter are essential in spectroscopy, sensing, quantum information processing, and lasers, however, there are further intriguing uses that could potentially lead to new exotic materials with revolutionary applications in the advanced quantum electronics industry.
In most of these applications, light is modelled as electromagnetic plane waves travelling at the speed of light in a vacuum. As a result, in quantum electrodynamics, light-matter interactions are usually viewed as quite weak and captured at the lowest order. However, advances in understanding the coupling of photons to material quasiparticles (plasmons, phonons, and excitons) highlight the need for a more comprehensive view of the photon as the fundamental unit of all light-matter interactions. In this new picture, the photon can have a wide range of polarization and dispersion while being limited to a few nanometres. In interactions with both bound and free electrons, such photonic quasiparticles permit a plethora of previously unobservable light-matter interaction events.
Electronic quasiparticles, on the other hand, are states in a material in which the collective behaviour of the electrons is the same as if there were free elementary particles with completely different properties than free electrons. Combining these distinct properties would allow us to not only isolate new forms of matter but also to industrially scale the manufacture of exotic materials and design metamaterials that would potentially be revolutionary and decisive in the next 100 years of technological growth.
Scientists at The Citadel have discovered a new class of unusual matter known as EM-636. This matter is mostly made up of quasiparticles, which do not behave exactly like their solitary analogs. They are classified as "strange" quasiparticles because, under certain conditions, they constitute the building blocks of a whole new exotic materials class: crystals produced by pairs and triplets of pure elements with revolutionary chemical and physical properties.
At room temperature, one can obtain Q-Bits from considerable amounts of exotic matter crystals which can be used as topological materials. Topology is a branch of mathematics that deals with structures and shapes which feature certain traits in common; this could be the key to the future architecture of light-driven Quantum Processors at room temperature.

The Jocaranda Copaia has been identified as the reference wood for the creation of highly performant micro- and nanocrystalline cellulose derivatives after three years of research and pilot engineering in new cellulose-based materials that may be employed in a wide range of industrial areas.
Exagon Industries was awarded a letter of intent (LOI) by the Asociacion De Produccion De Arabisco Nativo, Asoparabisco SA to be the primary contractor for the design, development, and implementation of a processing plant for MCC and NCC large-scale manufacturing in the province of Sucumbios (Ecuador). We appointed Ormus SpA of Santiago de Chile (Eduardo Frugone) as our LATAM representative and advocate of 4ENG Process Engineering Technologies, and they are now conducting all negotiations with the parties.
"The road will be long because the farmers' consortium does not now have the funds for project development," says George Terrel, the business leader of the Cellutech project at 4ENG Infrastructure, "but we are quite far ahead with the feasibility study and the required budget has been determined."
Natural fibers have piqued the curiosity of many people due to their renewable nature, enormous supply of raw materials, good mechanical qualities, and inexpensive cost. The cellulose found in plant cell walls can be separated and extracted, acting as a reinforcing agent in polymer composites to create lighter, more durable, and biodegradable composites. Acid hydrolysis techniques are used to isolate cellulose crystals using various acids, resulting in many different materials. In this work, the effect of the acid hydrolysis process, with hydrochloric acid (HCl) and sulfuric acid (H2SO4), resulting in MCC and NCC by one hydrolysis step, was verified and then analyzed for chemical and morphological features, showing considerable improvements on these qualities.
For the preparation of renewable resources, several techniques were examined, including physical, physicochemical, and chemical treatments. Most of these processes require high temperatures and pressures, as well as highly concentrated chemicals for pre-treatment. Alternatively, ionic liquids (ILs) - potentially appealing "green" recyclable alternatives to environmentally hazardous organic solvents – have been widely used as solvents, (co)solvents, and/or reagents in biopolymer processing.
SynteknaTM technique is based on MW in-process synthesis of selected ILs that may be used for direct MCC and NCC extraction, and it produces highly environmentally friendly, low-cost manageable, and high-efficiency results. When processing biodegradable composites, the SynteknaTM ILs method has numerous advantages over conventional procedures, including non-corrosiveness and non-volatility, excellent dissolution power under relatively moderate circumstances, and high thermal stability.
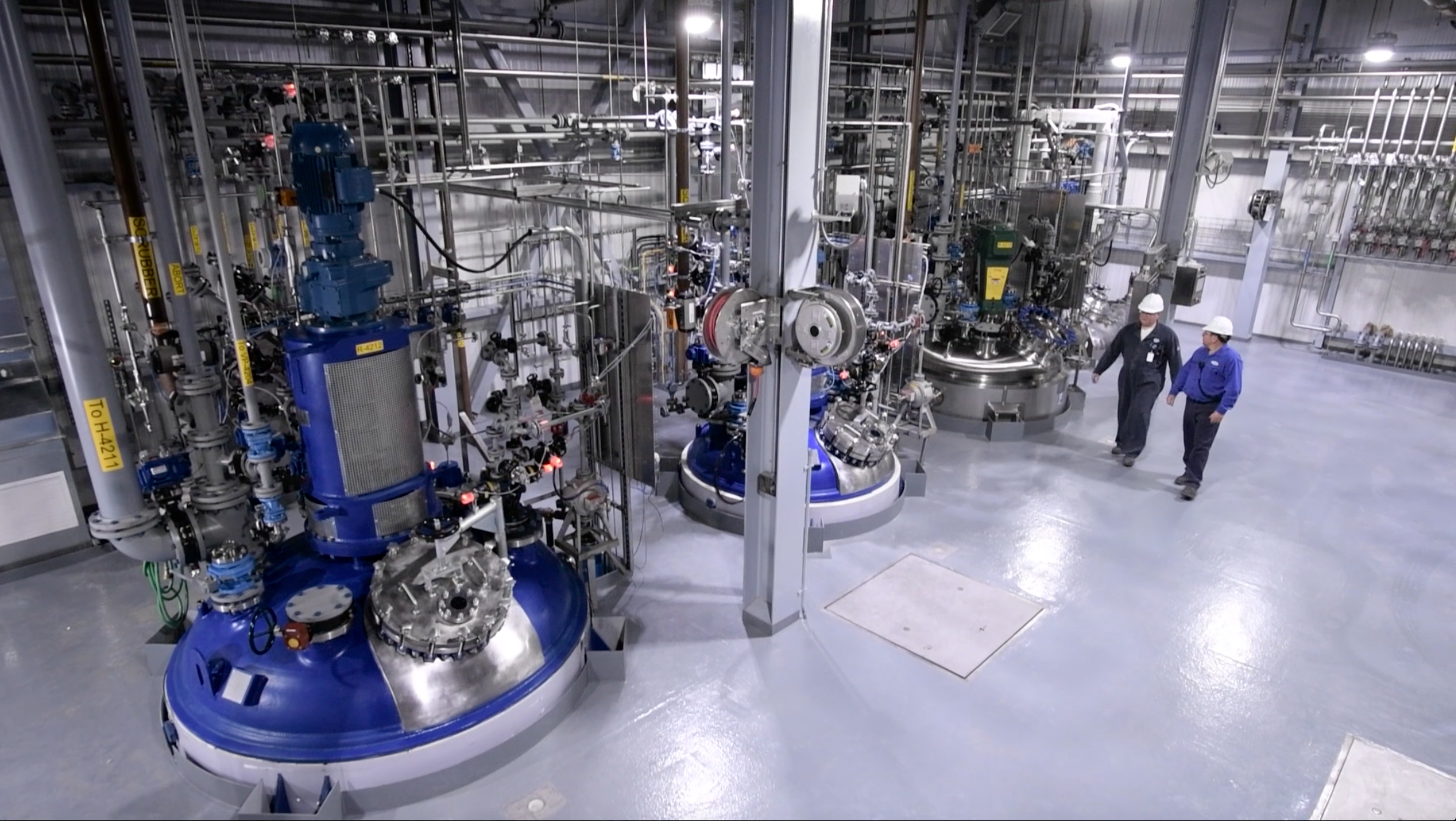
SynteknaTM is not a simple technology brand, nor is it a manufacturing technique like many others. SynteknaTM is an approach based on the Open System Science concept developed by Exagon Industries Ltd. The modular architecture that distinguishes SynteknaTM systems allows for the expansion of manufacturing plants without affecting the operations, as well as the reduction of management costs and the environmental impact.
The competitive advantage is expected to be significant by combining the action of AI with a breakthrough quantum-based core technology and the use of in-process ionic liquids synthesis and application.
In today's current processes, the brine is extracted by pumping and concentrating the lithium by one of two processes.
Adsorption with a selective lithium adsorbent (polyethylene glycol) first, then evaporation in shallow pools constructed for this purpose second. When a solution is saturated, evaporation can generate precipitation in addition to increasing the concentration of salts.
The benefits of adsorption include the fact that it is not affected by the salt water's composition (brine with a low percentage of lithium can be treated experimentally as if it were seawater) or the location's weather circumstances; also, there is little waste produced.
The downsides are that reagents are required, adsorption apparatus is costly and complex, and adsorbent costs are considerable.
The benefits of natural evaporation include the use of no energy and few chemical reagents, but it is limited to ore extraction rather than the synthesis of useful compounds; the disadvantages include the need to use another separation method at the same time, the accumulation of waste, and the reliance on local weather conditions (evaporation speed and rainfall).
The bottom line, current separation, and production technologies are little efficient and not long-term sustainable in terms of energy balance and operating costs. Our technology combines reversible catalysis with ionic liquids (ILs) and continuous high throughput flow synthesis, with microwave and sonification in three distinct phases. The synthesis of ILs (Phase 1) occurs in line with the process and is a separate module that is linked to the mineral purification system (Phase 2) and the attainment of targeted compounds (Phase 3).
This enables the ILs to be synthesized autonomously and at a cost savings of more than 30% when compared to the acquisition of the compounds and their relative application. The financial savings and infrastructure impact are significant, as are the preservation of the sites and the reduction of stress on the mine, giving a very advantageous short-term ROI and a very efficient profit margin.
Three custom processes and plants worth a total of $3.9 billion are now under consideration for our potential customers in the lithium processing business area. We are working hard to finalize these contracts, which are now in the feasibility phase.
4ENG Process Engineering intends to establish itself as a market leader in the design of processes and plants for the synthesis of new molecules and strategic materials with the new SynteknaTM systems, in the logic of the open system.